Featured Posts
Buy Lab Grown Diamonds: A Sustainable and Affordable Alternative to Natural Diamonds
Website Improvement and CMS Integration for Your Plumbing Business
Elegant Choices: Exploring Men’s Wedding Bands in Australia with Lab-Made Diamonds
Diamonds Wholesale Singapore: Your Ultimate Guide to Finding the Perfect Sparkle
Fax from iPhone: Upgrade Your Communication Instantly
Why Your Business Needs a UTM Solution
Effective Ways to Clean Sticky Residue Off Plastic Items
Crafting Audio Bliss: Your Guide to the Perfect Setup with Ultimate Stream
Optimal Strategies for Boosting Sales in Your eCommerce Business 7 Key Approaches
The Creative Possibilities When It Comes to Unique Sticker Papers
Exploring the Fifth Circuit Court of Appeals: An Insightful Guide
6 tips to promote your church revival event on social media
5 Core Benefits of Litigation Support
Trade Show Displays: Captivating Your Audience and Maximizing Your ROI
AI Art Generator: A Game-Changer in the Art World
Most Viewed
GogoPDF: The Ultimate Seamless Document Editing Tool
Anker Soundcore life note: The Best Audio Player For Creative Music Lover
Exploring the Fifth Circuit Court of Appeals: An Insightful Guide
What to Expect From Your Digital Marketing Company
The Impact of Science Fair Projects on Learning
How To Make Chicken Masala in A Steel Kadai?
Different Casino Games
How Can Electronic Signature Technology Help Your Business?
Enjoy Playing Video Games? If So, Read This
Effective Crypto Trading Strategies
The Creative Possibilities When It Comes to Unique Sticker Papers
How to get started with your favorite KuCoin Cryptocurrency
Why Are There So Many Cryptocurrencies?
Download Mobile App Here – July Boosts Charity
What Are Logistics Services?
Latest Posts
Buy Lab Grown Diamonds: A Sustainable and Affordable Alternative to Natural Diamonds
Website Improvement and CMS Integration for Your Plumbing Business
Elegant Choices: Exploring Men’s Wedding Bands in Australia with Lab-Made Diamonds
Diamonds Wholesale Singapore: Your Ultimate Guide to Finding the Perfect Sparkle
Fax from iPhone: Upgrade Your Communication Instantly
Why Your Business Needs a UTM Solution
Effective Ways to Clean Sticky Residue Off Plastic Items
Crafting Audio Bliss: Your Guide to the Perfect Setup with Ultimate Stream
Optimal Strategies for Boosting Sales in Your eCommerce Business 7 Key Approaches
The Creative Possibilities When It Comes to Unique Sticker Papers
Exploring the Fifth Circuit Court of Appeals: An Insightful Guide
6 tips to promote your church revival event on social media
5 Core Benefits of Litigation Support
Trade Show Displays: Captivating Your Audience and Maximizing Your ROI
AI Art Generator: A Game-Changer in the Art World
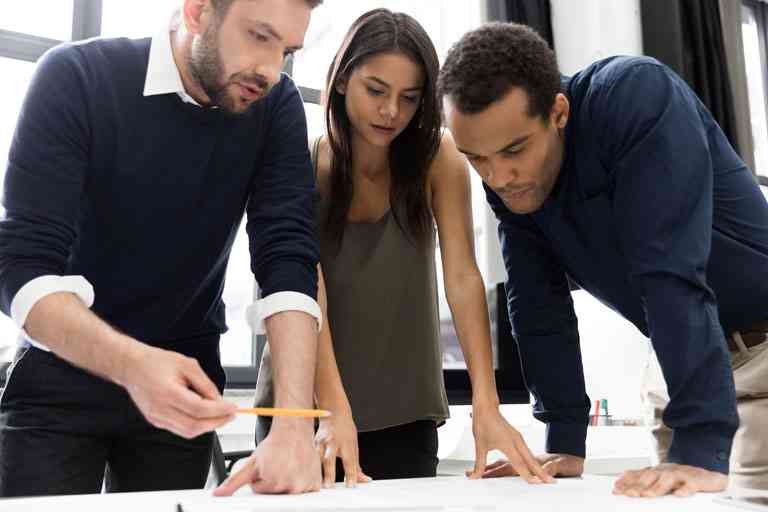
Safety programs provide guidelines and checklists that can make workplace environments safer by preventing incidents. Workers must be aware of the safety procedures that must be followed in their department or field.
Safety programs can cover a wide range of procedures, from repairs and maintenance to office space safety and even suggestions on avoiding identity fraud and using chemicals safely. OSHA has established healthcare standards to serve as a guide in creating and implementing a safety program for each organization. A safety program can only be effective if the work environment has been investigated and employees have been trained.
How to Establish an Effective Safety Program?
Establishing a successful safety program requires that employers understand their responsibilities under the Occupational Safety and Health Act. OSHA considers these requirements to be the foundation of any workplace safety program.
A safety program addresses a company’s urgent needs and provides long-term worker protection. The program should be implemented at the workplace once it has been designed. A safety program anticipates, identifies, and eliminates circumstances or practices that potentially lead to work-related accidents and illnesses.
Ideally, the process of developing an effective workplace safety program involves eight steps:
Make a Commitment to Stay Safe
Include safety in your company’s mission statement and involve leaders in the development of safety initiatives. These objectives should be written down so that they may be tracked and improved upon. This adjustment will assist in establishing a safety culture and keeping safety at the forefront of everyone’s minds.
Find out Your Industry’s Requirements
Review and check the OSHA resources and speak with other industry professionals. Also, sometimes it is beneficial to bring in an outside expert for your business, even if it is simply a safety manager from another company similar to yours.
Document the requirements and advice so you can track whether or not they are met.
Identify Possible Hazards and Dangers
Anything that has the potential to do harm should be dealt with. Talk to your colleagues and survey your own workplace to find out the ideal spots to make improvements.
Pay attention to workplace dangers such as shop layout, environmental risks such as dust, hazardous behaviors such as using machinery, and, ultimately, your company’s current culture.
Document these, as well as the points from Step 2, so that they can be addressed in the future.
Create Policies and Regulations
The policies and regulations should be adjusted to the needs and challenges identified in Steps 2 and 3.
They should also make both management and employees accountable for their actions when it comes to safety. It’s better if they’re written down and available to staff, and some even require one.
The following policies and regulations should be included for a safety program:
- Incident Management
- Audit/Inspection Management
- Health Management
- Knowledge Base/ Training
- Training Assignments
- Reporting & Analytics
These programs are fairly simple to manage in tools like those provided by CloudApper Safety.
Educate Your Employees
A decent rule of thumb is to train-
- New employees
- Employees who have just been transferred or assigned to a new position
- When a new process, substance, or piece of equipment is installed
- When new threats are detected
- Refresher training is required if it is deemed necessary
It is advisable to keep the training engaging and log any training that takes place using either spreadsheets or relevant software.
Investigate and Report Any Accidents and Incidents
Regardless of the severity, this will aid you in preventing future accidents.
Determine the source of the problem, identify potential improvements, then implement and track remedial and preventive measures. This may necessitate revisions to previously prepared documentation and training.
Through the CloudApper Safety App, it is easier to log any previous accidents and incidents that will help the employees to be careful and aware. Also, the training modules can be changed without any extra effort in CloudApper Safety App.
Review Your Program
Every year, go over your training, procedures, and any written safety paperwork you have to see if there are any flaws in your program and how you can fix them.
After making necessary changes, follow the same steps as before, but on a smaller scale.
At this point, having a robust auditing tool to go over every element of your safety program is beneficial.
Implement an OSHA Recordkeeping and Incident Management Software
Procedures, manuals, training, audits, incidents, and other tools should all be available in a good software package.
The Safety Compliance Applications like CloudApper Safety integrate workplace safety compliance issues into a single platform, allowing users to manage them more effectively and efficiently than before.
By digitizing all related data, you can save time and money on paperwork and administrative tasks for OSHA recordkeeping and compliance!
Author Bio: SK. Moinur Rahman is a digital marketing analyst at CloudApper. It is a No-Code Enterprise Mobile Apps Platform consisting of OSHA Recordkeeping & Incident Management Software, HIPAA Compliance Management Application, etc. He’s on a mission to stamp out gobbledygook and to make boring business blogs sparkle.
Written by Cheryl Waller
Trending Posts
Who Controls the Bitcoin Network?
What is ChromeDriver C# and How Do You Run It for Selenium WebDriver?
Huawei Watch Deals- Have A Fantastic Shopping Experience
What to Expect From Your Digital Marketing Company
Reasons Why Should You Split PDF Files
What You Must Know About White Label VoIP Providers
Easy Web Design Tricks You Must Know
How Are Lugged Valves Different from Wafer Butterfly Valves?
Book 12in M7 Before Purchase Must And Should Think Twice
[pii_email_f173a3874f9b9a484b24] in fix 2021?
What Opportunities Are Available To People With A Disability?
Things to Look For When Choosing a Sportsbook
Learn How to Code for Beginners
Everything You Need To Know For Passing The TOGAF ®9 Certification Training Test.
8 Best Online Tools for Office Workers in 2021
Most Viewed
CBD Oil for Dogs: All You Need to Know
Everything You Need To Know For Passing The TOGAF ®9 Certification Training Test.
Why Choose Cheap Internet In Mississauga?
MongoDB: Everything You Need to Know to Use the NoSQL Database
Play Online Slots at our Slot Machines
SEO Tips For Healthcare And Healthcare-Related Medical Sites
Solutions In Staffing Management
3D Lab Printer is Evolving Digital Dentistry
Find The Error [pii_email_6e8e157c1031f0c4b55e]
What to Expect From Your Digital Marketing Company
Design A Web Site With These Tips
Walk Me and their comparison with Pendo
Why Are There So Many Cryptocurrencies?
Benefits of CBD that can Serve as a Marketing Base
What is ChromeDriver C# and How Do You Run It for Selenium WebDriver?
Trending Posts
Buy Lab Grown Diamonds: A Sustainable and Affordable Alternative to Natural Diamonds
Website Improvement and CMS Integration for Your Plumbing Business
Elegant Choices: Exploring Men’s Wedding Bands in Australia with Lab-Made Diamonds
Diamonds Wholesale Singapore: Your Ultimate Guide to Finding the Perfect Sparkle
Fax from iPhone: Upgrade Your Communication Instantly
Why Your Business Needs a UTM Solution
Effective Ways to Clean Sticky Residue Off Plastic Items
Crafting Audio Bliss: Your Guide to the Perfect Setup with Ultimate Stream
Optimal Strategies for Boosting Sales in Your eCommerce Business 7 Key Approaches
The Creative Possibilities When It Comes to Unique Sticker Papers
Exploring the Fifth Circuit Court of Appeals: An Insightful Guide
6 tips to promote your church revival event on social media
5 Core Benefits of Litigation Support
Trade Show Displays: Captivating Your Audience and Maximizing Your ROI
AI Art Generator: A Game-Changer in the Art World
Popular Posts
Buy Lab Grown Diamonds: A Sustainable and Affordable Alternative to Natural Diamonds
Website Improvement and CMS Integration for Your Plumbing Business
Elegant Choices: Exploring Men’s Wedding Bands in Australia with Lab-Made Diamonds
Diamonds Wholesale Singapore: Your Ultimate Guide to Finding the Perfect Sparkle
Fax from iPhone: Upgrade Your Communication Instantly
Why Your Business Needs a UTM Solution
Effective Ways to Clean Sticky Residue Off Plastic Items
Crafting Audio Bliss: Your Guide to the Perfect Setup with Ultimate Stream